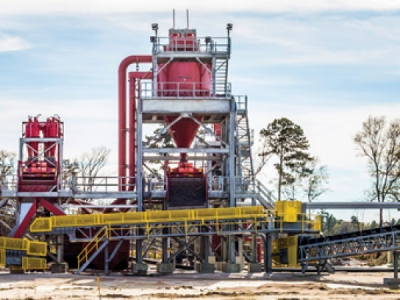
Posted on May 2, 2019
River Aggregates has been supplying aggregate products to customers in the Houston, Beaumont, and East Texas markets since 2011. It has two sand and gravel operations in Texas — one in Conroe, and a new one in Rye. The Houston area is growing at a rapid pace, creating a huge demand for building materials.
“There’s a lot of activity coming out in this direction,” says Rob Van Til, managing partner of River Aggregates, speaking of the market for the new Rye plant. “We think over the next 10 years, we’ll not only get into the north and east side of Houston, but we’ll also get into Baytown and the Port of Houston area, as well as Beaumont and a little bit of east Texas, with our material.”
As reserves at its old Romayor operation neared depletion, River Aggregates began the hunt for a new location. It found the perfect spot, just 4 miles from its Romayor operation near the small town of Rye, northeast of Houston. The location includes 1,300 acres of coarse sand and gravel and is expected to have a lifespan of 20 years. It is expected to yield 60 percent concrete sand and 40 percent fine sand after removing 5 to 8 percent gravel.
Let’s make a deal
The new Rye dredging operation is located on bottom lands near the Trinity River that once served as a pasture, but it didn’t happen overnight. Just a couple of years ago, River Aggregates’ Rye Plant was simply an idea being discussed with the landowner, Will Daniel, who envisions the land as one day being the location of his family’s dream home. Daniel spent a lot of time working out the details with River Aggregates before reaching an agreement.
The small pond on site was enlarged and filled with water before a new DSC dredge was brought in to begin working.
Daniel wished to capitalize on the land before turning it into a homestead. He was focused on timber production and cattle grazing leases, but knew there were several aggregate companies in the area, so he believed there might also be usable aggregate on his property. However, it was only a few years earlier that a major aggregate producer cored part of Daniel’s land and passed on the opportunity to open a mine there. Despite the prior rejection, he spoke with several other mining companies in the region, and ultimately pursued a deal with River Aggregates, which was willing to mine all the materials on the site, not just concrete sand, and was willing to work with him on a timeline for completion of mining.
“The process took about a year of conversations, talking, dreaming, and sharing concerns, hopes, and future ideas,” Daniel notes. “As a result, we’ve got a really good reclamation plan that supports our long-term objectives. Kudos to them for doing their homework. While other larger companies had the money to do so and chose not to, River Aggregates drilled my entire property, identifying a large source of reserves that extended beyond the area drilled by a bigger, well-known company that said it would be a “geological anomaly” for there to be reserves in the area where River Aggregates found them.”
In the end, it was a win-win scenario for both parties.
Setting up the plant
River Aggregates bought all new equipment for the operation, including a McLanahan Hydrosizer Plant and Ultra Fine Sand Plant. Hydrosizer technology allows for a better, cleaner cut between coarse and fine sand.
When it came time to set up the operation, Carl Davis, managing partner at River Aggregates, took on the job of designing and building the plant, but it wasn’t easy. There were setbacks.
“We had already made the agreement and had leased this place and were in the process of coming out here, but Hurricane Harvey slowed us down in getting everything ready to go,” he explains.
The company bought all new equipment for the operation, including a new DSC Dredge and a new McLanahan processing plant. When the land was leased, however, the type of processing plant had not yet been determined.
“The old processing plant at the Romayor location was what is considered a conventional sand processing plant consisting of a sand classifying tank and sand screws,” Davis explains. “But, we knew that hydrosizer technology was out there that would make a better quality product. McLanahan had the equipment we needed to make the sharp and consistent cuts required to make quality concrete sand.”
There was already a small pond on site, but it was enlarged and filled with water. The dredge was then put in, and the processing work began.
From the dredge, slurry is pumped through a large pipeline at approximately 6,000 gallons per minute to the primary plant, where it is pre-processed. It first passes through a velocity box, where the water settles before it proceeds to the primary screen. The primary plant kicks out the oversize and gravel, and the balance of the sand and water goes into the sump tank below, where it is pumped to a density separator.
“Basically, the density separator is a big round tank sitting at the top of the structure,” Davis notes. “All of the sand is pumped into two large cyclones, where the water and silts are separated to waste, and the sand slurry is fed into the hydrosizer. In the hydrosizer, a fluid bed of water about half way down allows the heavier sand to fall through, while the lighter sand spills out over a weir into the next section and goes on to the fine sand plant.”
The fluid bed is created by spray bars in the tank, which are fed by a large pipeline that brings in water from the pond at approximately 2,400 gallons per minute to provide a constant water pressure. The feed and water pressure have to be consistent.
“This is a new technology for us, but it’s not really new in the industry,” Van Til explains. “That [hydrosizer] technology lets you make a better, cleaner cut than you would with a classifier tank. It’s becoming more and more desirable, because it does a better job of making a more consistent grade of sand. We think we’ve probably increased our yield by 4 or 5 percent.”
“We knew that moving to the new hydrosizer technology was going to be a learning curve for us,” Davis adds. “McLanahan has done a great job of understanding what we want to do and helping us design and develop the plant that we know will do what we want in making concrete sand. We are able to offer a better quality product to our customers.”
Davis explains that both the concrete sand and fine sand circuits use McLanahan dewatering screens. He says sand that has been through a sand screw has 18 to 20 percent moisture, while sand that goes through a dewatering screen has only 10 to 12 percent moisture. The drier sand makes it easier to stockpile the sand and to load trucks more consistently.
“While concrete sand is our primary product, the Ultra Fine Sand Plant allows us to keep the fine sand particles out of the settling ponds and produce a fine sand we can sell,” Davis notes, adding that the sand plant features four separators that pull the water out of the slurry and send it back to the pond.
The control room or control center is located right next to the processing plant, so the plant operator can keep a close eye on everything without the need for cameras and monitors. The control room is also raised, so the operator can easily see the tops of the tanks.
“What I like about this plant is, today, I can walk in here, turn on the plant, and it runs,” Davis says. “It makes quality sand every day.”
“We spent a lot of time from an equipment and technology standpoint,” Van Til notes. “Carl has done a great job of building and designing a state-of-the-art plant.”
A bit of Texas history
During the Liberty County Bicentennial Observance in 1956, a marker was placed at Plantation Ranch to denote its rich heritage in Texas history.
River Aggregates is leasing a bit of Texas history for its new Rye Plant. The parcel of land is a part of Plantation Ranch, which has a long history dating back before Texas won its independence from Mexico.
After the American Revolution, Pvt. Aaron Cherry and his family left Virginia, eventually making their way to Texas in 1818. They settled on a bluff overlooking the east bank of the Trinity River and built a plantation. From there, Cherry traded with the Indians and the infamous pirate Jean Lafitte, who had a settlement on Galveston Island. In 1835, the Mexican government granted one league (4,428 acres) of land to Cherry.
Cherry played host to some of Texas’ greatest heroes in its fight for independence from Mexico, including Jim Bowie, William Travis, Davy Crockett, and Sam Houston. In 1936, the Texas Centennial Committee named the Cherry plantation the oldest permanent Anglo settlement in Texas. So, by the time William Partlow “Bill” Daniel and his wife, Vara Faye Martin Daniel, purchased the plantation in 1948 and named it Plantation Ranch, it already had a rich heritage.
“In Texas’ long history, the ranch has not changed hands much,” says Will Daniel, grandson of Bill Daniel and current landowner of the parcel of land being leased by River Aggregates. “Aaron Cherry sold it to the Ellis family, who sold it to the Cruse family, and the Cruse family sold it to the Daniel family. It’s worth noting that President Sam Houston appointed Ellis as ambassador to the Alabama-Coushatta Indians on behalf of the Republic of Texas. One can only imagine what the ranch has witnessed over its long history.”
Daniel says his grandfather discovered the plantation in the late 1940s while campaigning to be county attorney. Due to fuel rationing during World War II, his grandfather traveled the county in a horse-drawn wagon, which required him to stay overnight in the far reaches of Liberty County. On at least one occasion, he stayed with the Cruse family at their historic plantation.
“Poppa fell in love with it and set his mind on acquiring it someday,” Daniel says.
Even though his older brother, Price Daniel, made a career out of politics, serving as Texas’s attorney general, United States senator, three-term Texas governor, and justice on the Texas Supreme Court, Bill made his living off the land and as a country lawyer. Occasionally, he answered the call to serve, first as Liberty County’s county attorney, next in the U.S. Army, then in the Texas House of Representatives, and later as governor of Guam after being appointed by President John F. Kennedy in 1961, thus earning the enduring nickname ‘Governor Bill.’
After purchasing the plantation property from the Cruse family, Governor Bill continued to buy adjoining tracts of land, eventually making up nearly 3,000 acres of contiguous pastureland. At times, he ran up to 1,100 head of cattle on the ranch, which required a lot of help, especially when he was in Guam.
“Through the years, Poppa hired a lot of staff,” Daniel says, explaining that there were numerous buildings and houses on the ranch with several families living there. “It was a large cattle ranch, practically a small town itself, continuing its history as the ‘oldest permanent Anglo settlement in Texas.’”
Over the years, Governor Bill’s Plantation Ranch hosted many famous people, including Roy Rogers, Dale Evans, Loretta Lynn, Fess Parker, Roy Acuff, Kitty Wells, and a young Hank Williams Jr. It also hosted a retreat for United States astronauts and Russian cosmonauts during the Cold War. Partial planning for the original movie, The Alamo, took place there as well. John Wayne had his own bedroom in the “Big House,” and a longer runway was built so he could fly in and out. Governor Bill also provided and/or secured hundreds of longhorns and horses for the movie and appeared in three parts — a Tennessean, a Mexican, and the speaking part of Colonel Neill.
“The Ranch hosted annual Crippled Children’s Parties for many years to provide the children a day of fun, fresh air, shows, and a historical atmosphere — all free from my grandparents,” Daniel notes. “Another of the ‘big four’ family charity projects was the annual Easter Egg Hunt, to which everyone ‘young at heart’ in east Texas and west Louisiana was invited. School children would also come to the ranch as part of an elementary school field trip to learn about cattle operations and ranch management. The point is, this land has so much history behind it that was important not just to the family, but to the entire region.”
The Daniel family has been a big supporter of Baylor University in Waco. Governor Bill, and his father M.P. Daniel, made significant monetary and other donations that have been providing scholarships for students from Liberty and Montgomery counties who attend the university. In 1985, buildings from Plantation Ranch, along with thousands of artifacts from life in the late 1800s, were donated to Baylor by the family. The buildings include a cotton gin, blacksmith shop, hotel, livery stable, school-house, barbershop, dance hall, saloon, and town hall, as well as 25 horse-drawn wagons. Many of the historical items are now on display at the Governor Bill and Vara Daniel Historic Village, which is part of the Mayborn Museum Complex located along the Brazos River beside Baylor Law School.
Safety first
“At River Aggregates, safety is, and has to always be, our number one priority,” Davis says. “Since we are regulated by MSHA, we tailor our safety training and documentation to those requirements.”
The Rye Plant crew consists of the plant manager and eight employees. Everyone who works at the plant, or its sister plant, is involved in regular safety meetings and refresher training. At each plant, at least one 15-minute safety meeting is held every week first thing in the morning to cover current safety issues.
Safety meetings are also held once a month and are designed to be interactive, Davis says. At the meetings, they cover refresher subjects and discuss new issues encountered at any of the company’s operations. The company also uses Westward Environment safety trainer to help with the monthly meetings. The net result is a successful safety program.
Equipment List
- DSC dredge
- Caterpillar 972 front-end loaders (2)
- Caterpillar 349 excavator
- Caterpillar D6T dozer
- Caterpillar 745 haul trucks (2)
- McLanahan Hydrosizer
- McLanahan Ultra Fine Sand Plant
Source: aggman.com