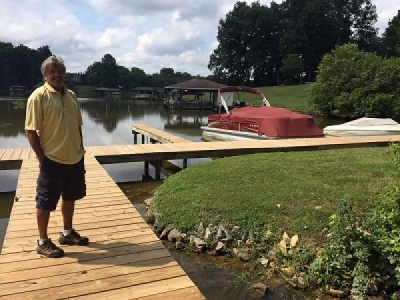
Posted on August 16, 2018
The community dock at your lakeside community doesn’t do much for your recreational boating plans if it’s inaccessible due to a long-term buildup of silt.
That’s the problem Troy Crites and his Southwind Shores I neighbors at Lake Anna were facing. Crites has owned his property for about 20 years, but for the last decade or so, the community dock had been useless. The sediment had piled up so high that weeds and grass were growing in the boat slips.
That all changed between last fall and this past spring thanks to hydraulic dredging, an environmentally sound and minimally invasive technique that has made the community dock and its 10 slips usable again. Such projects at Lake Anna are permitted only between October and March.
“There are about two dozen communities around Lake Anna with this problem that have started the permitting process and we’re the only ones who have gotten the job done,” Crites said during a recent tour of the site.
Crites, who is president of his community’s homeowners association, wanted to find an alternative to typical mechanical dredging, which uses a heavy excavator to scoop out the silt and fill countless dump truck loads to be hauled somewhere off-site.
He discovered a small Ruther Glen-based company called Pajic Construction, which specializes in hydraulic dredging. The building and excavation company was started by Joe Pajic in 2008 and is co-owned by him and his son, Nick.
Pajic gained an affection for the water while serving as a game warden for the state Department of Game and Inland Fisheries, retiring as a captain in 2015 to focus fully on the business. A friend had introduced him to hydraulic dredging, noting that it would be a useful technique in any of the 85,000 ponds and lakes in Virginia.
“We actually vacuum up the sediment, which causes less turbidity in the water than scooping the sediment out, so it’s better for the environment,” Joe Pajic said.
The 6-foot-wide dredger is tethered to the shore by a cable and pulled back and forth over the dredging area. It has the ability to get under boat house roofs to dredge covered slips. Working within narrow slips is no problem, either.
The project is also done entirely on site, so there’s less air pollution from truck exhaust and less wear and tear on the shoreline and the rest of the site without trucks moving in and out. Pajic calculated that keeping the sediment on the site avoided moving 130 dump-truck loads.
The Pajics’ excavator moves across the surface of the lake and, using a 65-horsepower Cummins diesel engine, pumps the sediment through a flexible 6-inch pipe to an elevated prepared site above the shoreline.
The site, an acre or so of nearby available land, was excavated to make room for two 80-foot-long geotextile “dewatering tubes,” which are described as very heavy-duty bags made of weed-stop-like fabric that is porous to let water drain out. Hay bales surround the excavated area to prevent runoff, per Chesapeake Bay rules.
Organic polymers incorporated into the fabric help retain pollutants within the tube. The draining water follows a path back into the lake.
“The water that drains back into the lake is actually cleaner than what we pumped into the bag,” said Pajic. Between the filtering of the dredged water and limiting turbidity, water quality is compromised as little as possible as work proceeds.
After one bag is filled, it is left to drain while the other is being filled in an alternating system. Once the water drains from a bag and the dredge spoils are compacted, there’s space for more sediment to be pumped in.
Pajic said the amount of water a particular type of soil will hold can be calculated to determine the volume of drained sediment he’ll end up with. In this case, almost 2,600 cubic yards of sediment in the dock area became about 1,800 cubic yards after it drained, a ratio of about 70 percent.
Earth that was removed and set aside to make room for the bags was then put back on top of them, creating a 3.5-foot cap of soil, as required, that was then hydro-seeded to keep it in place. When The Free Lance–Star visited the site in July, it was being mowed for the first time.
“We always like to leave a site ready for a good secondary use,” Pajic said. This site now blends in with the grassy field surrounding it and can be used for recreation or even have a community picnic pavilion built on it, if that’s what residents want.
THE PREPARATION
Before any of this took place, two things had to happen. First, the residents had to agree to pay for it, and second, the proper permits had to be acquired.
The Pajics’ bid was about $100,000, of which about $8,000 was earmarked for the permitting process. Crites said each homeowner agreed to pay a $4,000 special assessment, which was added to some of the HOA’s cash on hand. He said the cost of roughly $50 per cubic yard of dredged material was in the target range for such projects.
The permitting process involved four entities: the Army Corps of Engineers to meet federal regulations, the Virginia Department of Environmental Quality and Spotsylvania County for state and local rules, respectively, and finally Dominion Energy’s requirements as the owner of the lake. Spotsylvania and Dominion provided the closest supervision given the relatively small size of the project.
How long the impact of the dredging will last is uncertain. “Only Mother Nature knows the answer to that question, as it depends on storms, and their severity, lake levels …,” said Crites. “We hope to buy a decade or more.”
Ways to prevent future buildup would be complicated and expensive, so Crites tried to do his part by placing a few truckloads of stones along the shoreline as riprap.
“I put some sweat equity into it,” he said. “But it’s all good.”
Source: fredericksburg.com