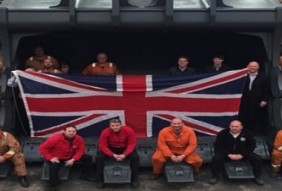
Posted on May 24, 2016
By Robert Gibson, ChronicleLive
A family-run business based in Sunderland has been tasked with manufacturing the largest ever excavator buckets to come out of the UK, in deals worth almost £2m.
In November last year, Hi-Spec Manufacturing – a division of Birtley’s MST Parts Group – secured a £1.6m contract with a leading dredging company requiring four buckets for use with a Backactor 1100.
It has already produced three – two of which are 20m cubed in size and a considerably larger bucket measuring five metres tall and weighing 44 tonnes. The latter is due to be collected shortly.
A further so-called ‘ripper bucket’ of 9m cubed, then, will complete the order.
Dredging companies use excavators through mounting them on large vessels.
Hi-Spec Manufacturing’s latest order follows another, worth £300,000, from a different company for a single bucket destined for use with the biggest backhoe excavator in the world, the Caterpillar 6090.
Rory Whitehall, a director at the company, said: “We usually work with the likes of Hitachi and Komatsu, focusing on areas like quarrying and construction.
“But every now and then, these massive dredging companies will come along with these big orders – and that’s always good news for us.”
MST Parts Group was established in 1971 by Mr Whitehall’s grandfather, Kenneth Whitehall
Three years ago, the company separated its parts reselling business from the manufacturing side, now based at the Pallion shipyard in Sunderland.
Mr Whitehall, who said he felt “very proud” that his family’s business was now the only one in the region involved in the manufacture of large-scale buckets, explained that it took around 14-16 weeks to make each one through a process requiring high levels of skill.
“Usually, the dredging companies will send us designs as a starting point,” he said.
“But we have our own in-house design team and we’ll be asked to change this or that, make this lighter or that lighter.
“Once we’ve got the sign-off on the design, we’ll order our Swedish steel – the best in the industry – in different thicknesses, which will be cut into sections like flat-pack furniture.
“When that is ready, fabrication can begin and that point everything is welded by hand, taking care the steel is heat treated to the right temperature.”
The shipyard, he explained, was an ideal location for such work as, when the buckets were finished, there was sufficient space to move them into place using large cranes.
“Trying to get the welders and develop them to high standards is a big part of what we do,” Mr Whitehall said.
“We are lucky in a sense; there’s not much work going around for welders at the moment due to the fortunes of subsea oil and gas.
“We’ve also got a good team in place.”
Source: ChronicleLive