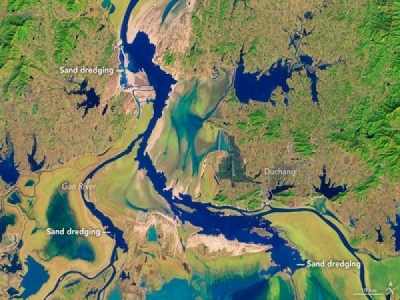
Posted on September 18, 2018
China—the world’s fastest-growing economy with the largest population—leads the world in cement production, the critical ingredient that has built China’s mammoth cities, sprawling roads, and other infrastructure. China pours 60 percent of the world’s cement; the country’s production in 2011-2013 surpassed U.S. production for the entire 20th century. While it paved the way for Chinese growth, it came at a dangerous cost: 1.6 million Chinese citizens die each year from respiratory illnesses linked to small particulate matter emissions, of which 27 percent come from cement production.
Coal fuels energy-intensive cement plants, making these plants the top industrial source (up to 18 percent) of the nation’s CO2 emissions. It takes 200 kg of coal to make 1 metric ton of cement—and in 2010, China produced nearly 1,868 million metric tons of cement, representing a whopping 10 percent of the nation’s total coal consumption.
Excavating sand—a critical input for cement—adds to the environmental costs. “Most of the nearly 50 billion tons of sand and gravel mined or dredged every year is used to make concrete. That’s more than enough to blanket the entire state of California,” said Vince Beiser at a Wilson center event on the overlooked global sand crisis. In his new book, The World in a Grain: The Story of Sand and How it Transformed Civilization, Beiser reports that the world consumes more sand than any other natural resource except air and water—and we are running out of it.
For Shanghai’s skyscrapers, sand miners dredged sand from the bottom of the Yangtze River, “pulling out so much sand that it created a serious threat to flood control, undermining the health of the river,” Beiser said. After sand dredging was banned in other areas, mining companies dredged Lake Poyang—once a biodiverse basin in central China—now the poster child for the irreversible destruction of China’s construction boom.
China and the world cannot afford the environmental and climate costs of cement production
Ultimately, China and the world cannot afford the environmental and climate costs of cement production. China’s recent war on pollution has not yet cleaned up the cement industry, but there are encouraging signs in a confluence of efforts by the Chinese government, businesses, and grassroots groups to nudge this hard-to-reform sector towards a greener path.
What Makes It So Hard for China to Reform Its Cement Industry?
Since the 1950s, all 31 provinces in China have developed their own cement enterprises to decrease transportation and distribution costs, and keep profits local. Cement production exploded in the 1970s to fuel the country’s urbanization, and continued to expand even as urban construction started to slow in the past few years.
“Ever since the 2008 global financial crisis, the Chinese government has used investment in infrastructure, real estate, and industrial capacity as a way to stimulate the economy,” Greenpeace’s Lauri Myllyvirta states in an interview, “That’s what is behind the mind-blowing amount of cement the country uses.”
Even as the national government raises concerns over cement overcapacity, local governments—especially in China’s Rust Belt—fear social unrest and political risks of job losses in the cement sector and often find loopholes to continue subsidizing the industry.
Breaking the Logjam on Cleaning Up China’s Cement
China’s leadership has implemented harsh measures to mitigate environmental degradation caused by the cement and other energy-intensive industries. The 11th Five-Year Plan mandated aggressive energy-efficiency goals for the country’s top 1,000 most energy-intensive industries. China’s cement industry was previously dominated by polluting and energy-intensive vertical shaft kilns. The campaign reduced the share of these kilns to only 20 percent by 2010, and prompted existing plants to become more energy-efficient, but overall emissions from the sector remain high.
Political pressure on the cement increased when China’s leadership declared a war on pollution
Political pressure on the cement, coal, steel, and other polluting industries increased when China’s leadership declared a war on pollution in 2013, establishing ambitious targets and deadlines for reducing emissions and ramping up punishments for local governments that evaded the targets. And the 13th Five-Year Plan mandated a 25 percent cut in the number of cement enterprises by 2020.
The hammer came down in March 2018, when the newly formed Ministry of Ecology and Environment launched its Blue Sky Campaign to more quickly cap China’s air pollution and carbon emissions. In early June of this year, the ministry deployed 18,000 inspectors to impose new regulations on the cement industry.
Paving a New Path Forward, Yet Potholes Abound
“For the survival of the cement industry, producing at ultra-low emissions is a must for the near future,” said Tonny Xie of in an interview. Yet becoming more efficient remains a challenge. Small firms struggle to comply with new regulations, due to the high costs of retrofitting and long returns on investment. A chinadialogue report highlighted one solution: namely, that local governments could push Chinese cement enterprises to merge and reduce the financial burden of these upgrades.
Lawrence Berkeley National Laboratory is investigating electrifying cement kilns to reduce cement’s immense carbon footprint. WWF-China has pushed energy-efficiency measures and alternate fuels such as waste straw, used car tires, and municipal waste for cement kilns. While these fuels are potentially cleaner alternatives, Anders Hove of said in an interview that “the high operating costs for creating collection and delivery supply chains of these alternative fuels can be difficult and costly, requiring cooperation between government agencies that regulate waste and the industries.”
The Chinese government’s heavy investments in carbon capture, utilization, and storage could be used for cement and other heavy industries. Similarly, the upcoming national carbon emissions trading program could help to create financial incentives to push the most inefficient cement plants to finally close.
Real estate companies are also using the market to pressure cement industries to green their production. In 2016, the Chinese Foundation Society of Entrepreneur and Ecology (SEE) joined forces with major Chinese real estate companies and associations to create China’s first-ever green supply chain certification system targeting building materials. Many of China’s top developers have signed onto the program and by 2020, SEE estimates that green-sourced building materials will reduce the building sector’s annual CO2 emissions by 50 million.
Lessening the environmental footprint of sand dredging to satisfy the hunger for concrete buildings and road construction in China and the rest of the world remains a tricky problem. While scattered companies and researchers are developing stronger and “self-healing” concrete, there’s no affordable, commercial-scale alternative for sand, said Beiser—but “we can be smarter about our access to it, and our usage of it.”
Source: NewSecurityBeat