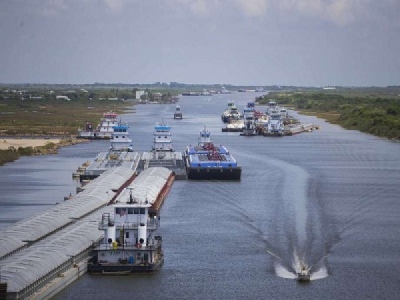
Posted on September 26, 2017
By Andrea Rumbaugh, Houston Chronicle
Container ships bound for Houston called on other ports as Hurricane Harvey slogged its way across the upper Texas coast and into the history books.
For weeks after the storm’s massive floodwaters receded, trucking companies lost revenue and endured delays.
And still today, a heavy buildup of silt is blocking many of the barges that ply the Gulf Intracoastal Waterway between here and Corpus Christi in service of the region’s sprawling petrochemical industry.
The devastating storm brought one of the nation’s busiest transportation hubs to a halt, and supply chain disruptions are still reverberating. Executives and port officials have yet to put a final tally on the delays, although one observer says it easily could total $2.5 billion as the hurricane struck a complex network of modern manufacturing, where the supply chain has become a de facto warehouse.
Explained Capt. Mike Cunningham, director of program management at the Greater Houston Port Bureau: Product comes off a ship, is loaded onto a truck and then delivered directly to the assembly line.
That system has begun to recover – admirably, some say – but interviews with several big players suggest it may be awhile before Harvey’s havoc is fully behind them.
“It disrupts everything,” Cunningham said. “Everybody has to make different arrangements, and that increases costs.”
Disruptions to the so-called inter-modal system began before Harvey came ashore near Rockport the evening of Aug. 25. By then, the U.S. Coast Guard had closed the Port of Houston, so cargo wasn’t coming in or out. Sixty-three of the 102 ships that were scheduled to enter the port between Aug. 23 and Aug. 31 were diverted elsewhere. Trains, trucks and barges were similarly idled.
Among the ships caught in the reshuffling was the Philadelphia Express, whose Houston-bound containers were unloaded in Savannah, Ga., owner Hapag-Lloyd said. Likewise, Maersk Line reported that two of its vessels dropped off cargo in Freeport, Bahamas.
Port Houston Executive Director Roger Guenther expects much of the diverted cargo to find its way onto other vessels and wind up in Houston through the port’s two container terminals, which are back open.
“It still ends up in our port, just on a different ship,” he said.
Guenther emphasized the importance of getting the port up and running by highlighting the immediate impacts on consumers when the Houston Ship Channel was closed: The price of gasoline went up, the supply of jet fuel fell sharply, and stores were eager to be restocked.
Channel lost 3 feet
Meanwhile, the Ship Channel lost 3 feet of depth. To put that in perspective, a previous study says losing 1 foot of depth costs the U.S. economy as much as $280 million a year.
The U.S. Army Corps of Engineers has embarked on a roughly $20 million dredging project. Chris Frabotta, deputy chief of the operations division in the Corps’ Galveston District, said work is underway to remove shoaling in mid-Galveston Bay area and will expand to the Bayport Container Terminal area and upper Ship Channel.
Guenther said the City Docks, where steel is unloaded, lost as much as 5 feet in depth. The Corps of Engineers had just finished dredging that section after flooding in 2015 and 2016 had likewise dumped silt into the area.
Moving forward, Guenther said he will push to dredge deeper and wider “to catch some of the silt that comes in there and not be as impactful after a flood.”
Cost of closing
Maria Burns, director for the Logistics and Transportation Policy Program at the University of Houston, said closing a major port like Houston for a week could cost up to $2.5 billion from delayed or canceled business transactions throughout the supply chain.
“This amount could be even higher because Texas also is involved in other states’ supply chain,” she said. “We serve as the transit state to import or export commodities that affect other states as well.”
Much of the losses can eventually be recovered once the delayed cargo arrives, Burns said, but the additional staffing and equipment to handle the sudden influx can eat into profits.
She encouraged all parties involved to study their warehousing and systems to protect against flooding or wind damage and to heed the lessons before the next major storm. She said the supply chain rebounded quickly, but damage to roads and other infrastructure is hampering recovery.
“This extreme event highlighted where our vulnerabilities are,” she said.
Railroad work
Railroad companies, which like trucks distribute the shipped-in products to warehouses around the country, experienced their own shutdown due to the tropical deluge.
Union Pacific, for example, halted inbound trains the Saturday of the storm, and heavy flooding eventually put some 1,750 miles of track between Brownsville and Beaumont out of service. Repair and inspection crews had brought all but 50 miles back online by Sept. 7. All the tracks were restored as of last week.
As soon as the work was complete, trains converged on Houston.
“All of those trains that were waiting, we were now funneling them into Houston as best as we could,” Union Pacific spokesman Jeff DeGraff said.
Volumes have since normalized, but Union Pacific is expecting another spike in traffic as more manufacturers and refineries come back online.
Harvey’s effect on the petrochemical industry also can be seen at places like Katoen Natie’s Houston warehouses, which are currently 35 percent to 40 percent empty. The typical vacancy rate is between 5 percent and 10 percent.
Katoen Natie packages plastic resins for exporting. These resins arrive in rail car and are packaged in bags and boxes. This is typically a 24/7 operation, but the company is currently running 16 hours a day, five days a week. Some days have only eight hours of work, as some plants shut down during Harvey have yet to resume production of plastic resins.
Those that are back in operation are supplying U.S. customers first, leaving Belgium-based Katoen Natie to wait for the overseas shipments it handles.
“We just need to hunker down and keep our costs at a minimum in order to get through this,” said Frank Vingerhoets, president of polymer operations in Canada, Mexico and the U.S.
Intracoastal Waterway
The industry’s return to capacity is similarly affected by Harvey’s impact lower on the coast. Silt buildup where the Intracoastal Waterway meets the Colorado River, near Matagorda, has prevented barges from traveling between Houston and the Corpus Christi area. Many have sat idle at the intersection.
It’s common for barges to leave one port with a refinery’s feedstock and travel the Intracoastal to a different port, where another plant will use that feedstock to create its own product. The silt blockade is raising concerns that plants won’t get needed feedstock in time.
“Some of the refineries and some of the plants may have to shut down as a result of not getting enough feedstock and materials,” said Jim Stark, president of the Gulf Intracoastal Canal Association.
The 12-foot-deep waterway was reduced to just 3 feet in the section between the west Colorado River Lock and the Colorado River, Frabotta said. Two other sections near the locks also require dredging, at a total cost of some $7 million.
On Tuesday, Frabotta said the Corps of Engineers hoped to open the locks with a draft restriction of 8 feet on Saturday. It hopes to allow ships with 9-foot drafts on Sept. 30, 10-foot drafts by mid-October and the full 12-foot draft by early November.
Permitting 8-foot drafts could allow empty barges to cross, though it likely won’t get much of the loaded barge traffic moving.
“A lot of those barges that are waiting there probably have more than an 8-foot draft,” said Matt Woodruff, director of public and government affairs for Houston-based Kirby Corp., the country’s largest operator of tank barges.
Trucking companies
Trucking companies, which shoulder much of the container load at the port, took multiple blows.
Houston-based Overland Express Co., which owns or contracts with about 65 trucks and moves containers between the port and mostly local customers, reported that many of its trucks sat idle because their drivers were busy taking care of swamped homes.
The water also damaged equipment. Consolidated Chassis Management said flooding affected about 40 percent of its 1,500 Houston-area chassis – the steel frames with tires that hold containers – that were on the street and in local depots during the storm.
“We’re tight on equipment,” said Jon Poelma, senior vice president and chief operating officer of the company, which manages a Gulf regional pool of about 17,000 chassis that are owned by leasing companies and ocean carriers. “We’re not short on equipment. We’re able to meet the needs of the market right now, but that was due to a lot of advanced planning and quick reaction after the hurricane.”
Consolidated Chassis Management continues to reposition its chassis from storage areas to rail terminals and ports. Some were brought into Houston from other regions along the Gulf. Maintenance partners worked overtime and weekends to repair damaged equipment.
Michael Dyll, CEO of freight-forwarding company Texas International Freight, said flooded chassis have made it difficult to find equipment needed to haul containers.
Driving for FEMA
Flatbed trucks, which don’t require chassis, can also be used to haul containers. But Dyll said those drivers were lured by the Federal Emergency Management Agency’s higher rates during the week after the storm.
Dyll had to pay drivers from outside the region. And since more goods were entering the city for rebuilding than the normal flow of traffic leaving Houston, drivers were initially charging more to cover the cost of returning home empty. They were also charging higher rates because they still believed Houston was underwater, even though much of that water had receded.
Noël Perry, partner and transportation economist at FTR Transportation Intelligence, said truck drivers out of their normal routes may have to drive more empty miles or have more downtime between loads.
“When they’re out of route, they have to charge more,” Perry said. “And sometimes it’s difficult to get the customers to pay more.”
To help truck drivers pick up or drop off containers, Guenther said Port Houston opened the truck gates on Labor Day and one Saturday, dates they usually wouldn’t be open. He said wait times have been normal for the drivers.
‘We’re sacrificing’
Yet Gary Conner, president of the Houston Transportation Professionals Association and director of sales for Overland Express, said he noticed increased congestion with long lines extending outside the gate.
He said it usually takes an hour for truck drivers to get in and out of the port. Since Hurricane Harvey, it often takes two hours or more.
Dyll, like others in the industry, said Hurricane Harvey has squeezed his company’s margins and is having an impact on its customers.
“We’re sacrificing a little bit,” he said, “and we’re asking our customers to pay more.”
Source: Houston Chronicle