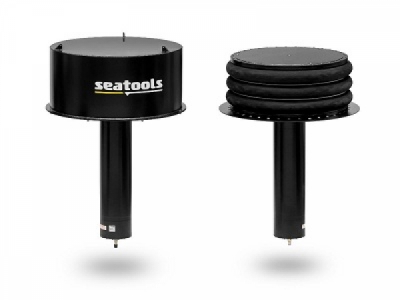
Posted on January 27, 2018
On behalf of its client Bakker Sliedrecht, subsea technology company Seatools completed the development, manufacturing, and testing of two 250-liter subsea pressure compensators. The compensators will be applied to 1.7 MW submersible electric motors installed on a new hopper dredger currently constructed by Wenchong Shipyard in China for the Chang Jiang Waterway Bureau (CWB).
Over the course of several decades, the units will operate in harsh environments characterized by vibrations, shock loads, dirt, and temperature changes. Therefore, the ultra-long lifetime compensator design was selected. This durable design is simple yet effective, and showcases extreme mechanical robustness. Robustness, that additionally, facilitates relatively large overpressures, resulting in a minimum risk of water ingress. The design also limits the number of dynamic components exposed to seawater, allowing the compensators to endure long-term, submerged application and ruling out the need for maintenance.
Jan Frumau, Managing Director at Seatools, is pleased with the successful delivery of the compensators. He said: “Our experience as subsea equipment manufacturer confirms the importance of adequate pressure compensation to guarantee the reliability of subsea equipment. With the ultra-long lifetime compensator series we offer a compensator design that reaches new robustness and reliability levels. In fact, we believe the range is becoming the new standard for this type of capital-intensive subsea equipment. To find a reputable company like Bakker Sliedrecht affirm this and choose our pressure compensation solution, makes us feel honored.”
The application demanded a low pressure gradient, which had to be met within narrow tolerances. These criteria were set to create the most favorable conditions for the motor seals, thereby assuring the integrity of the seals (and therefore the motor) in the long term. To meet these requirements, detailed modelling of various conditions that the compensator encounters in the field, have been performed. Later, modelling was verified by means of an extensive testing program. Testing and subsequent analysis on non-linearity, holding pressure, and hysteresis (among others) showed that the compensator met all stringent pressure tolerances well within the prescribed 0.05 bar.
SOURCE: www.Seatools.com