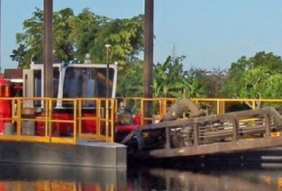
Posted on April 28, 2016
By Kendra Wingate, Minuteman News Center
The Mill River cleanup project continues and officials recently announced it has successfully reached its significant goal of the removal of lead impacted sediment through hydraulic dredging. After water quality data confirmed a portion of the Mill River had been identified as impaired for aquatic life, shellfish and recreation due to bacteria, lead and chromium, a cleanup project was begun and led by former site tenant, the Excide Group, Inc.
The site, located at 2190 Post Road, was formerly home to the Excide battery plant, which opened in 1950 and produced automobile batteries until it discontinued operations in 1981. The approximately 6.32-acre property is owned by The Excide Group, Inc. which has been tasked with remediation of the lead contamination on the property and surrounding waters.
Excide prepared a Sediment Remedial Action Plan in an effort to remediate the affected areas in compliance with a Department of Environmental Protection (DEEP) consent order. The requirements of this order included the mapping and remediation of lead impacted sediments in five Mill River Study Areas: between Interstate 95 and the railway, between the railway and the Post Road, between the Post Road and Harbor Road/Tide Mill Dam, below Harbor Road and the dam into the Southport Harbor and above Interstate 95 to Mill Hollow Park.
According to the DEEP fact sheet, the cleanup was to necessitate the hydraulic dredging of approximately 27,000 cubic yards of lead impacted sediments to achieve established cleanup goals, the use of geotextile tubes to dredge the slurry dewatering system, a dewatering filtrate treatment system with discharge of treated water back into the Mill River in accordance with the National Pollutant Discharge Elimination System (NPDES) permit, and dewatered sediment transported off-site for final disposal at approved landfills.
Excide announced that the sediment dredging portion of the project has been completed. Site preparation was conducted in July 2014. A hydraulic dredge specifically designed for environmental work was used to remove lead impacted sediment from the river beginning in October of 2014 as contractors complied with dredging restrictions designed to protect the marine life and also complied with weather delays. The contaminated sediment then flowed through a processing area; a dual wall floating pipeline carried dredged sediment from the river to the sediment processing area located on the property. This onsite sediment processing area included dewatering aid conditioning, very large geotextile tubes (currently filled with a surveyed number of approximately 27,000 cubic yards of sediment) overlying a gravel dewatering pad lined with two layers of high density polyethylene to drain the water from sediment and to contain the water and sediment within the area, filtrate treatment tanks, and a pipe through which the clean, treated water is then sent back into the river.
Now in the projects final phase, the last of the dewatering of sediment and treatment of filtrate will culminate throughout the next few weeks, monitoring and sampling, as required by CT DEEP, will continue. The contaminated dewatered (dry) sediment will be removed; transported via trucks lined with plastic and covered to prevent sediment from escaping, to pre-approved off-site disposal areas. Upon completion, the processing area will be dismantled and the site will be restored. The “Load Out” is currently scheduled to run through June.
Trucks will access the site from I-95 via exit 19 and the route will be coordinated with the Town of Fairfield Engineering Department. Some 40-60 truck trips are planned per day, 5-6 days per week. It is anticipated the loading and removal of dewatered sediment will take 3-4 months to complete. Operations will comply with noise levels set in the Town of Fairfield codes, dust and odor will be also be monitored.
“Our goal is for the whole project to be completed by, barring any unforeseen issues, the end of October 2016,” said Barry Culp, Remediation Project Manager at TRC. TRC has had onsite staff monitoring the operation in an effort to be proactive in preventing inconveniences to the general public.
READ FULL ARTICLE HERE