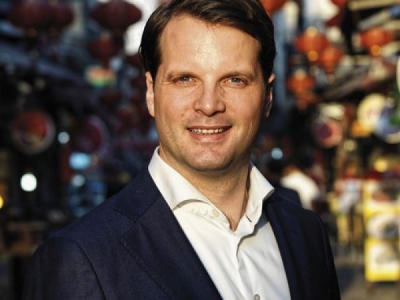
Posted on May 17, 2020
Over the past 100 years, Bakker Sliedrecht has made a major contribution to the growth of the dredging industry. DPC talks to managing director Sjoerd Teertstra about hybrid systems, automation, new types of fuel, and the safe transition to zero-emissions shipping
Bakker Sliedrecht has become one of the largest independent electrical system integrators in the world with 300 employees, a 12,000?m2 workshop in Sliedrecht, the Netherlands, and, among others, an office as well as a service hub in China.
Sion Bakker founded the NV Electrotechnisch Bureau S Bakker in 1919 and over the past century it has come a long way. “We were the first company to develop a submersible motor that drives dredgers’ underwater pumps and suction tubes,” managing director Sjoerd Teertstra told DPC, “and we also led the development of water-cooled drive systems. Now we strive to be a forerunner in the future too”.
Bakker’s journey began at his workshop, which at the time was located at the Rivierdijk in Sliedrecht. He began by installing central heating systems in churches and offices as well as providing industrial buildings with electric lighting. However, it only took a year in business for the young company to turn to the maritime industry.
“Bakker started to focus increasingly on the dredging and maritime industries,” Teertstra explained. “In 1920, for example, his company installed electric lighting aboard steamship Gränna, which was built at the former Baanhoek shipyard in Sliedrecht. The electric installation for bucket dredger Kil followed in 1922.”
Expansion continued, but then came the Second World War, and on 10 May 1940, the German army invaded and occupied the Netherlands. “Our company was mainly closed throughout the war,” Teertstra said. “I really can’t tell you anything about that period, there’s simply no information.”
However, after liberation in 1945, Bakker Sliedrecht turned its full attention to electrical installations for ships, especially dredgers. “The maritime order portfolio became increasingly full and the projects more complex,” Teertstra continued. “As a result, the company expanded, building a new workshop and office block in 1951, and moving a little further along the Rivierdijk.
“During the devastating North Sea flood of 1953, Bakker Sliedrecht’s skills enabled it to help the Dutch industry, especially with the drying and reinstatement of electric motors. It also hired new, highly skilled technical staff during that period, and by 1955 had 20 employees.”
Effectively electric
Sliedrecht developed itself through the years as the cradle of the Dutch dredging industry and has established a pioneering reputation for advanced technology. When the Dutch and Belgian dredging contractors expanded in the region, Bakker Sliedrecht expanded too.
“The more efficiently they are able to work, the more successful dredgers become,” Teertstra noted. “As electrical installations aboard ships began to play an increasingly important role in driving efficiency, Bakker Sliedrecht became ever more closely intertwined with the dredging sector.
“Later, the offshore sector emerged and the same thing happened – increasingly complex ships that were, and are, dependent on electrical solutions. With our technology and systems, we have made an important contribution to making these sectors more effective.”
Even though the company’s workshop and offices were expanded and modernised, by 1970 they were still too small to meet demand. Bakker Sliedrecht bought land on the Nijverwaard industrial area in Sliedrecht and in December 1973, moved to its current location at Leeghwaterstraat. Sister company Bakker Repair + Services was founded in 1975 to meet the increasing demand for maintenance in all sectors.
During this period, Bakker Sliedrecht found a new generator and engine supplier in Spanish company Indar. The partners developed their own powerful submersible motors – both air-filled and oil-filled – that can be customised for any type of dredging vessel and enable work at depths to 250?m. Through its China operation, Bakker Sliedrecht annually equips several Chinese dredgers with such motors.
“We can adapt them to any type of dredger,” Teertstra said, “hopper, cutter suction, or crawler. What makes the motors unique is a special seal that enables them to work at such great depths. In addition to dredgers, deepsea excavators use our underwater motors for mining, while salvage ships use them in salvaging sunken vessels”.
In recent decades, Bakker Sliedrecht has been involved in the construction of dozens of ships, enabling the company to build close relationships with various Dutch shipyards. Even when shipbuilding moved to lower-wage countries in Eastern Europe and Asia, Bakker Sliedrecht’s specialists travelled with it. “Over the years we’ve adapted ourselves to geographical shifts. As a result, we can now supply and maintain our systems on all continents,” said Teertstra.
The company also looks to aid continuity for existing and potential customers. “For example, the ABB ACS 600 water-cooled drive system is becoming obsolete,” Teertstra said, “making spare parts difficult and costly to obtain. Bakker Sliedrecht has created a retrofit kit, the ABB ACS 880, to replace the ACS 600 while keeping its functionality. “Installing the ABB ACS 880 for a 1,800?kW drive system takes about a week.
Its key element is the water-cooled module that’s installed in the existing cabinet using a mechanical kit that fits the exact cabinet dimensions. Existing cabling in the cabinet is connected to the new ACS 880 module to save time and costs and minimise disturbance to other parts of the vessel. Spare parts for the ABB ACS 880 will be available for at least 15 years and will thus ensure the availability of customers’ electrical drive system.”
Future innovation
Bakker Sliedrecht won the Dutch ‘Pon Innovation Award’ for Best Innovation Process in 2015. Teertstra noted that such innovative power is highly needed now that the maritime sector is moving towards zero emissions. “We’re preparing all our systems and technology for hybrid and dual-fuel solutions, along with other types of marine fuel that ensure zero emissions. They all have an enormous impact on the onboard systems, both for new and existing vessels.”
Bakker Sliedrecht has been the first to develop a common diesel generator protection system (CDGP) for dual-fuel vessels that have DP (dynamic positioning) systems 2 and 3. The CDGP system has been successfully tested by classification society DNV GL.
Vessels that sail in DP2 or DP3 mode are required to maintain their position at all times, even in the event of failures or malfunctions. Power plants are usually divided into independent isles to prevent malfunctions, although this makes generators run inefficiently – which is why ships prefer to operate with generators in parallel operation.
“To prevent these from interfering with each other, a generator safety system is necessary,” said Teertstra. “Our CDGP uses software to detect and disable an ‘unhealthy’ generator before it can affect ‘healthy’ generators and make the entire power plant unstable. For power plants equipped with dual-fuel generators, this is much more complex as such engines behave differently than diesel engines and can unexpectedly switch from gas to diesel. The company’s CDGP system is now so well developed it can be deployed aboard dual-fuel heavy-lift vessels.”
Since 2018, Bakker Sliedrecht has partnered with RH Marine, which specialises in electrical systems and automation solutions for, among others, naval vessels and superyachts. One result of that, announced in October 2019, is a system that optimises the operational costs of a vessel’s diesel generator-battery hybrid power plant by incorporating a flywheel. This innovation reduces the installed battery capacity but increases its lifetime – with the result that a vessel’s total cost of ownership (TCO) decreases, but the reduced fuel consumption remains intact.
“For the load profile of a hybrid cutter suction dredger, implementing a flywheel can have a major impact on TCO minimisation,” Teertstra noted. Teertstra confirmed that the flywheel was being fitted into a specific dredger, but its name is confidential.
Source: dredgingandports