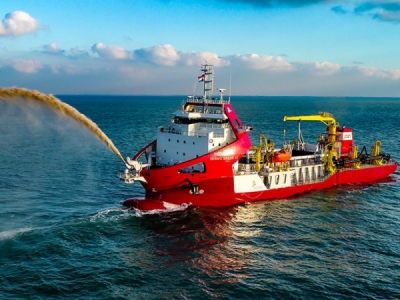
Posted on February 11, 2020
By Judith Powers, Special Correspondent to DredgeWire
In 1977 when I began reporting on the dredging industry,innovations were being made in the United States that would lead to a complete revolution in equipment, methods, companies and the market itself.
Positioning
At that time, dredges and survey boats were positioned using long range navigation (LORAN), with on-board receivers computing signals from a network of transmitters maintained by the governments of maritime nations. To zero in on specific working areas, a technology known as range-range positioning enabled operators to position dredges and survey boats more accurately bytriangulation, using shore stations at pre-surveyed locations that communicated their positions to receivers on the vessel, which then computed a series of boat positions using software provided with the system.Manufacturers of electronic equipment were coming up with equipment and software that would integrate the information required to conduct a dredging project. These included the dynamic position of the dredging tool on the bottom, the position and heading of the dredge, the records from the pre-dredge survey that indicated the x, y, z (latitude, longitude and depth) readings, heave, pitch and roll, as well as tide and river stage readings, to come up with an accurate map of the bottom. Much of this information was stored electronically, but much of it, such as survey lines and dredge position, was on printed charts, some of which were still created by hand-entering soundings on paper charts.
Because the lucrative oil and gas industry depended on the same technology for building offshore platforms and placing pipelines, these innovations didn’t depend only on the relatively small dredging market to fund research and development.
In the hydrographic survey sector, the method of using single beam sounders traversing a channel in increments as much as 50 feet left gaps in the survey that could contain debris, rocks or other high spots.
In 1977, Wayne Ross delivered two multi-channel sweep systems consisting of a range of transducers mounted on booms extending from the sides of a survey boat. This system would travel longitudinally the full length of the channel and produce a seamless record of the project. Ross commented that this method would become necessary as larger vessels with deeper drafts began using the shipping channels, that could be damaged by hitting the debris or shoals missed by single beam surveys.
To this day, Corps of Engineers districts in the navigable rivers are using Ross’s sweep systems, with sometimes a third generation of the boats recently delivered.
Ross began experimenting with digitizing depth signals in 1969. His work was the precursor to a leap in survey and dredge positioning accuracy that would take off in the 1980s. Digitized signals from echo sounders and other sensors were soon being incorporated by computers into many useful reports.
Dredging Companies
Dredging companies that handled the federal contracts in the United States in 1977 were often family owned and operated and worked almost exclusively in their own geographic areas. They consisted of less than a dozen large contractors that ran dredges capable of maintaining the deeper channels in the nation’s waterways. Dozens more smaller contractors that operated shallower draft dredges bid on contracts in shallow channels and in confined areas of ports. Inland, a number of companies maintained trailerable dredges that could be mobilized on inland lakes and shallow rivers, settling ponds and irrigation canals.
A major segment of the industry worked sand and gravel operations in areas where a high-water table flooded pits and made dry mining impossible. The Midwest had a vast aggregate deposit over several states which, combined with a high-water table, provided a fertile field for aggregate dredging. These producers depended on dredge manufacturers that could build for individual deposits and provide a steady source of wear parts for the dredges that worked in abrasive materials day in and day out.
The environmental remediation projects the federal government had begun to contract stimulated the rise of companies that specialized in handling contaminated material, which had been stabilized at the bottom of ponds and that was processed through a closed hydraulic system and the contaminants removed before the remaining material was placed in an appropriate, safe site.
Port Deepening
The 1980s saw a program to deepen the channels in the country’s major ports, authorized at first by the Water Resources Development Act (WRDA) of 1986, which also heralded the beginning of local (state and municipal) cost sharing for federal port and navigation projects – a concept unheard of prior to that. The ports and states protested vigorously against cost sharing, but over time it has become an accepted norm.The annual federal budget conversation was changed to include cost sharing percentages in all authorized projects, and dredging efficiency became more of a priority in the bidding process and in dredge operation. Funding of projects, with local funding included, required project owners to answer to local populations as well as the federal government to justify the money allocated for them.
Hopper Dredges
No private companies owned trailing suction hopper dredges in the United States in the 1970s. The work requiring this equipment was done exclusively by the U.S. government-owned hopper fleet. This was considered necessary for emergencies. The Corps of Engineers wanted control over the fleet so it could mobilize immediately in case of emergency. The dredging contractors believed that they could commit to mobilizing at the government’s request if needed, and that the federal government should not be competing against private industry for routine dredging contracts.
Great Lakes Dredge & Dock, American Dredging Company, T.L. James& Co., Inc.,C.F.Bean Corporation, and Williams-McWilliams Co.were adding trailing suction hopper dredges to their fleets in the 1980s by partnering with Dutch and Belgian dredging companies. These companies provided expertise and funding to the extent allowed by the Jones Act for foreign ownership of a vessel plying U.S. waters. Their hopper dredging entities were North American Trailing Company, Atlantic Trailing Company, Gulf Coast Trailing Company, and Stuyvesant Dredging Company, respectively.
Manson Construction & Engineering Company in Portland, Oregon designed, financed and built two split-hull hopper dredges with no outside participation.
These companies put pressure on the Corps of Engineers to divest itself of its hopper fleet and allow private industry to do the work. The Corps eventually reduced its hopper fleet and opened significant work to the private hoppers.
Once private contractors were bidding on hopper jobs, they negotiated with the Corps for a greater share of the annual hopper contracts, which resulted in formation of the Industry/Corps Hopper Dredge Management Group (ICHDMG) to provide an open forum between contractors and the USACE to discuss the allocation of contracts and any other issues related to the hopper dredge mission in the U.S.
The group meets regularly in conjunction with other dredging meetings and is open to all who have an interest in the subject.
GPS Arrives
Charles Trimble had taken up the option on the global positioning system (GPS) technology in the early 1970s when developer Hewlett-Packard opted not to pursue that market. Once the U.S. started launching its Navstar constellation of satellites, which transmitted positions to GPS receivers located on broad swaths of territory, Trimble began producing land survey systems that could achieve accuracies within several meters.The hydrographic survey and navigation industries also had an interest in the technology, and a section of the company – Trimble Navigation — worked with hydrographic surveyors and dredging companies to provide receivers and software that could provide positions on moving vessels.
The dredging and hydrographic survey industry watched this technology, attending conferences and workshops devoted to the technology, but continued using the range-range positioning systems that had proved to be accurate and robust in bad weather and to continue operating after taking a bad beating.
In December 1991, Fraser River Pile & Dredge Company (FRPD)in Vancouver, B.C. was the first to operate a dredging and hydrographic surveying operation using only GPS. The Trimble equipment was provided and installed, and training provided by Rentec of Houston. FRPD’s Dredging Project Manager Jan Oskam had learned about GPS at a Western Dredging Association meeting in 1990 and moved immediately to utilize the technology. This was the first use of the technology with no backup by range-range positioning systems. Its success eliminated a network of shore stations that took up to 12 hours a day for a full-time company employee to maintain and provided up to 1.5-meter accuracy in positioning.
Industry Associations
The dredging industry was represented in Washington D.C. by two advocacy groups – The American Association of Small Dredging and Marine Contractors (AASDMC) and the National Association of Dredging Contractors (NADC), representing large contractors. The two groups were at odds over the allocation of federal contracts and the Small Business Administration (SBA) Set aside Program. In 1988, the small business size standard was raised from $9.5 million annual revenue to $13.5 million. In its annual project allocation plan, the U.S. Army Corps of Engineers set aside certain federal navigation dredging projects to be bid on only by small businesses in order to “level the playing field” for contractors who didn’t have the assets to allow bidding at a less than profitable level in order to get a contract. Large contractors objected to the program as unfair to them because it deprived them of the opportunity to bid in a portion of the market, they saw themselves as having a right to.
In late 1993, the two organizations joined to form a single advocacy group called the Dredging Contractors of America (DCA), appointing Mark Sickles, previously director of the NADC, as executive director and Walter LarkeSorg, former director of the AASDMCC as assistant director. The purpose of the merger was “to strengthen the industry by representing more companies from more states than either of the former associations, utilizing each member’s energy more effectively,” the group stated in a news release.
Building a Better Clamshell
Digging tools used in dredging had remained unchanged for decades, some for centuries.
Clamshell buckets especially had not been subject to design change. Mounted on a crane, the two-part bucket is lowered to the bottom in open position. Closing the bucket using hydraulic rams or cables causes the bucket to dig into the bottom. The filled bucket is then raised by the crane and emptied into an adjacent barge.
Environmental dredging projects demand a minimum of turbidity to be created while dredging contaminated material, and the action of a conventional clamshell causes a suction when it leaves the bottom, causing a plume of turbidity.
In May 1992, Ray Bergeron introduced his Cable Arm Clamshell to the dredging industry. His fabricated bucket presents a wide, flat footprint that closes to a point that does not create turbidity when raised from the bottom. The closing mechanism is a system of cables and sheaves that lift the center, drawing the sides together in an even movement along the bottom. Once closed, the bucket seals, and little material escapes as the bucket rises in the water column. It is lightweight enough to allow a large capacity bucket to be used on a crane rated for a smaller bucket. It provides a mechanical digging alternative in environmental projects and a more efficient excavation of soft materials in conventional dredging projects.
Consolidating the Market
In the 1980s. the dredging market began consolidating. On the West Coast, the owners of Manson-Osberg ended their partnership and separated into two companies, Manson Construction & Engineering Company and Osberg Dredging Company, each taking one dredge. Manson Construction & Engineering Company acquired Reidel International and the dredging assets of Western-Pacific Dredging Company, thereby joining the ranks of the large dredging companies.
In February 1993, Weeks Marine, Inc., a small mechanical dredging company in Cranford, N.J.acquired the dredging assets of American Dredging Company of Camden, N.J., one of the large dredging contractors that had been a mainstay in federal contracting on the East Coast. Weeks also entered a beach renourishment partnership with Bean Horizon Corporation for operation of Bean’s dustpan dredge “Beachbuilder.”
In March 1995 T.L. James & Company, Inc. of Ruston, Louisiana, which had previously acquired Williams-McWilliams Dredging Company, announced at its annual shareholders meeting that it planned to shift its dredging and marine operations and assets into an independent, wholly owned subsidiary named T.L. James Marine Group. In November 1997, the company chairman G.W. James Jr. announced that the company would sell its marine and general contracting units, and in October 1998, Weeks Marine announced that it had acquired most of the dredging assets of T.L. James & Company.
With this purchase, Weeks added the dredges George D. Williams, the Tom James, the Arkansas the BTD-51 and the Natchez, bringing its cutter fleet to eight, a water injection dredge and three clamshell dredges to its fleet. On May 15th, Weeks acquired the hopper dredging operation Gulf Coast Trailing Company, including the hopper dredges Ouachita and Mermentau, which joined the R.N. Weeks for a hopper fleet of three.
This purchase made Weeks Marine and Great Lakes Dredge & Dock Company, Inc. the dominant large dredging contractors in the U.S. Gulf and East Coasts from Brownsville, Texas to Maine
In the T.L. James sale, Great Lakes Dredge & Dock Company acquired the cutter dredge Bill James, re-christened the Texas, and the Pontchartrain, re-christened the Arizona. B + B Dredging Company purchased the hopper dredge Mermentau’s sister ship Atchafalaya.
Changing the Safety Culture
A historically high injury rate on dredging projects, and a number of heart rending fatalities brought about a concerted effort on the part of the dredging industry to jettison the fatalistic approach to safety the industry had always had – that injuries are inevitable – and to instigate a program aimed at eliminating dangerous incidents and injuries. In 2002, the DCA created a safety program and hired a professional safety consultant to head it. The group teamed up with the Corps of Engineers, which had its own safety manual and safety regulations affecting dredging projects conducted by government contractors. Called the USACE/DCA Standing Safety Committee, the two groups worked to improve the safety practices in the industry.
In a further step, individual companies, with GLDD as the first, signed onto a revolutionary safety program entitled IIF – Incident and Injury Free – that aimed at changing the work attitude of company employees, eliminating the “good old boy, macho” toward safety and injury, and focusing the attention of everyone in the company on the goal of making sure everybody goes home safely at the end of the day. Ignoring hazards and engaging in unsafe behavior could be a firing offense. A person in the humblest job had the authority to remind a company officer if he or she was engaging in unsafe behavior.
Other contractors followed suit, some generating their own safety programs. The Western Dredging Association instituted annual safety awards, and companies began posting statistics of hundreds or thousands of man hours with no reportable injuries or incidents. No longer were unsafe antics or short cuts tolerated on a dredging project.
Dredging Organizations
The Western Dredging Association (WEDA) was formed in 1979 as a continuation of the World Dredging Conference (WODCON) established by Mort Richardson in1969. Its purpose was to provide an industry-wide forum and networking opportunity for dredging contractors, suppliers, consultants, the Corps of Engineers and government entities involved in dredging. WEDA was part of the new World Dredging Association (WODA) that was in turn divided in the Central Dredging Association (CEDA) in Europe and North Africa, the Eastern Dredging Association (EADA) covering the Middle East and Asia, and WEDA, covering North and South America. The dredging industry in Europe had organized CEDA, and attended the Ninth World Dredging Conference, held in Vancouver, B.C. in October 1980. At that meeting, WEDA and CEDA members helped Australian and Japanese attendees to organize EADA.
Starting that year, the World Dredging Conferences were held every three years, alternating among the three regions, and offering members the opportunity to meet colleagues from all over the world and to see projects in those areas.
The sand and gravel dredging companies were represented by the National Stone Sand and Gravel Association, a vibrant organization that held regular aggregate dredging seminars in locations where the group could visit a local dredging operation, and where vendors would present descriptions of equipment, subject to informed and frank questioning by the attendees.
The group held periodic conferences entitled the Concrete and Aggregate Producers Convention (ConAgg), at which equipment was displayed, and where the dredge manufacturers found a niche. In early 1990, The group paired with the general construction industry at its convention in Las Vegas. CONEXPO-ConAgg, held every three years, is a monstrous fair of large and small equipment attended by 150,000 and more people, who take over Las Vegas for the week, joined by dredging contractors in town for the annual Association of General Contractors (AGC).
Today
The business structure, technology, procedures and culture that changed so much in the 1970s, 1980s and 1990s have matured and continued in the 21st century.
“Sound in water” pioneer Wayne Ross died in 1997, and his son and longtime colleagues continued running the company, and his multibeam boats are still being used by the Corps of Engineers on the nation’s rivers. The system of mounting transducers in a line on retractable booms has continued to be the best method for doing condition surveys of navigable river channels, and his concern about deeper draft vessels plying our waters has come true, especially in the coastal ports, where multibeam surveys are a must for safe navigation.
The relationship between the Corps of Engineers Civil Works Division and the nation’s dredging contractors retains a fraught element, and the ICHMDG meetings feature frank discussions, but the changes hammered out between private industry and the Corps in the 1980s have created a basis for keeping the government fleet healthy for emergency purposes, and for maintaining a stable private dredging market that allows investment in new dredges and retrofit and improvement of existing equipment.
The safety programs begun in the industry at the turn of the 21st century have continued, with the conversation expanded to focus on details such as the proper gloves for any project, clothing for winter projects, as well as daily “required attendance” safety meetings on dredges, assignment of a safety coordinator for each dredge, and pride in winning WEDA safety awards. While numbers of incidents and accidents can be counted, the number of incidents that did not occur can only be estimated. The fact that the safety culture has been institutionalized (it is hoped) on most dredges and other facilities in the country can only mean that there is an assurance of safety where one did not exist before the program.
Once a promising but untried technology, GPS has now become the standard positioning technology in the industry, allowing for sub-meter and sometimes centimeter accuracy. With digitization of all measurements, and sophisticated software that can create any needed operational or production record, equipment and processes have been eliminated. Control rooms are not crowded with equipment and wiring. Reports are dependable and make dredging operations more efficient.
Swath survey technology, in which one transducer emits a fan of beams to produce a solid reading of the bottom has eliminated the problem of gaps in channel surveys.
In 1992, the Ports of Los Angeles and Long Beach announced their “2020 Plan”, for channel deepening, land reclamation and infrastructure in the adjoining ports. Now that 2020 is here, reclamation, deepening and infrastructure are largely complete, and the ports are in the midst of the “2018 – 2022 Plan” to assure the Port’s competitiveness and ongoing success. All other coastal ports are in the process of being deepened, spurred by the competition for deep draft ships allowed through the improved Panama Canal.
What lies ahead for the dredging industry is undoubtedly more channel maintenance, more beach renourishment, and more remediation of coastal storm damage. The improved dredges and supporting technology will allow these tasks to be fulfilled in a timely manner. Other dredging functions such as the vast aggregate dredging industry in the U.S. and the dredging and remediation of contaminated material benefit from the technological advances and the increasingly sophisticated scientists and engineers that have devoted their researches to dredging.
This article is the exclusive property of DredgeWire and cannot be modified, copied, reproduced, sold, or distributed in any manner or medium without permission from DredgeWire.