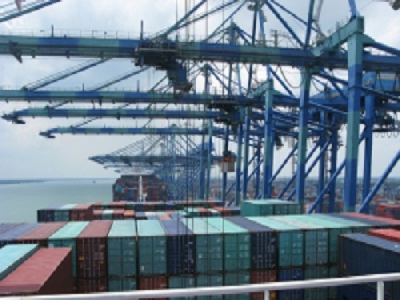
Posted on March 13, 2017
News is piling up about the continuing saga of chassis shortages. While the major US ports struggle to locate chassis, here in the Heartland the crisis fluctuates by region.
For example, Iowa exporters need both chassis and containers to get their products to the international markets they serve. But the question remains how Iowa shippers can locate the chassis and containers they require.
For the broader Heartland region, Rick Held, President of Held & Associates said, “It hasn’t been a big issue from our experience. More than likely the shortage is more pressing at the heavier traffic areas (port cities). We may be shy some during harvest or when there are heavy import shipments during holiday times. But mostly it’s a nuisance and not an issue.”
In Long Beach, for example, JOC.com reports the following. “The question is, what can we do as an industry to improve chassis utilization, not just what one player can do,” Bill Shea, CEO of Direct ChassisLink Inc. Mr. Shea’s comments were directed at the “pool of pools” arrangement in Southern California, but many ports and inland distribution hubs experience chassis availability issues to some degree.
As the largest US port complex, with about 80,000 chassis moving between the 13 container terminals and distribution facilities and rail yards in the region, Los Angeles-Long Beach grapples with chassis shortages at some locations, excess chassis at others, an unacceptable level of out-of-service chassis and excessive equipment dwell time to a greater degree than most regions.
Chassis imbalances are a way of life in Los Angeles-Long Beach. Four of the terminals hold 43.5 percent of the total inventory at the 13 container terminals, but they serve only 27 percent of the total demand, according to the pool of pools that was set up to manage chassis operations in Southern California. The remaining 56.5 percent of the inventory held by the other terminals must serve 73 percent of the demand.
The three major IEPs — DCLI, Flexi-Van Leasing and TRAC Intermodal — on March 1, 2015, made great strides in relieving the chassis mess that resulted when ocean carriers exited the business of providing chassis to BCOs. They launched the grey chassis arrangement known as the pool of pools so that now the equipment in each of their individual pools is interchangeable. This means that a chassis used to carry a container for one shipping line at one location could be reused to carry a container belonging to another line at another location.
Possibly if 100 percent of all of the chassis in Southern California were pool of pool chassis and shipping lines and BCOs all maintained the same business practices, there would be no problems today, but in the complex harbor environment that is not the case. Some terminals hoard chassis. Most ocean carriers give preferred BCO customers extended free time for holding on to chassis at their distribution facilities. Most lines also designate a specific chassis provider that must be used by BCOs for “store-door” moves on through bills of lading to the customers’ warehouses. Chassis maintenance and repair practices vary from terminal to terminal.
Shea therefore urged all of the industry sectors to work through the supply-chain optimization task force formed by the two ports to come up with standardized business practices in which each party may have to give up something for the greater good of the harbor complex. At a pool of pools meeting last week in Long Beach, the IEPs, terminal operators and ports formed a smaller steering committee to push the process along more quickly.”
Source: IBNewsmag