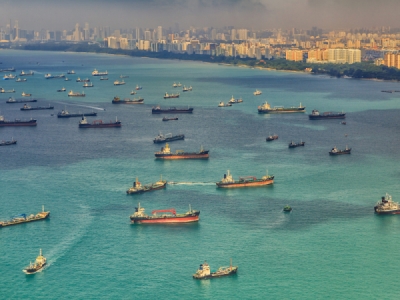
Posted on June 3, 2020
Many vessels spend time in challenging and complex environments, or are deployed in difficult operational profiles, where hull fouling can have a marked impact on efficiency and raise fuel costs. Various circumstances can prove challenging from a hull performance point of view and require proper attention since the current solutions on the market struggle to address these problems. Also, operational profile factors outside coating tolerance such as speed, activity and temperature can be encountered for a variety of reasons.
Bulk carriers, tankers and general cargo ships can spend long periods in ports being loaded and unloaded. Some of them may also be prevented from berthing for long periods due to neap tides. In such cases, shallow water and temperate environments can lead to accelerated fouling. Many shipowners must deal with these challenging operations on a regular basis.
The lower the predictability in operations, the higher the risk for fouling
Many ships have unpredictable trading patterns and must find cargoes where they can. That can mean that after operating in an area such as the North Atlantic with a coating chosen for that environment, the ship is then switched to tropical zones. Offshore ships face similar problems with periods of high activity followed by long idle times and operation in different climates. The lower the predictability in operations, the higher the risk for fouling on the ship’s hull, potentially leading to increased fuel consumption and higher environmental impact.
Coatings are usually developed for specific operating conditions meaning their anti-fouling performance is highly probabilistic. Any changes to the expected operating conditions will mean the coating will not perform as expected. The main factors that increase the probability of fouling are long idling periods under unfavourable conditions such as location and duration.
Frequent hull cleaning required to maintain performance
There are numerous anti-fouling coatings on the market today offering different technologies tailored to differing operating profiles. Ships using the best coating technologies suited for normal, predictable trade will not require cleaning between drydocking. However, as operations become more challenging, frequent hull cleaning will be required to maintain performance.
The increased fouling levels accompanying challenging operations limit the owners’ operational flexibility, because fouling increases downtime (for inspection and cleaning), fuel cost and other unpredictable costs. They also risk speed-claims for ships operating under time charters. Excessive biofouling on the hull may also restrict access to some ports or even territorial waters especially in the Pacific where ships have been expelled from ports in some cases.
Source: jointherevhullution