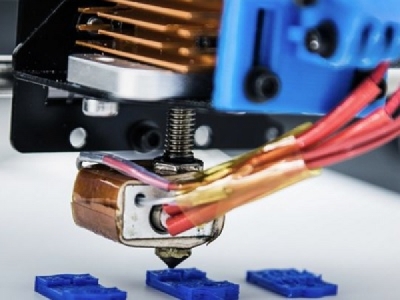
Posted on January 22, 2019
The Wall Street Journal quite recently ran a story with the striking headline, “Get Ready for 3-D Printed Yachts.” The story centered on a Dutch entrepreneur, Maarten Logtenberg, who has created the largest printer in Europe, the CFAM. His creation is also the largest 3-D printer incorporating glass and carbon fiber in its design, anywhere.
Logtenberg has targeted the maritime industry throughout his efforts leading up to the public launch of the CFAM. And the first two sales, the WSJ tells us, were to yacht manufacturers.
WHAT’S THE FUSS ABOUT?
The news these days is full of 3D printing, and of the growing sense that 3-D printing constitutes the ultimate in disintermediation. Even if we don’t have any near-term expectation of small household printers rolling out, say, automobiles: certainly the plants that do make automobiles will in the not distant future print out many of their own parts, eliminating the need for much inventory management. Repair shops, too, might be in a position to manufacture their own parts on site, leading to marked changes in that industry.
Meanwhile,the medical uses of 3-D printing have become notorious, largely because the television show Grey’s Anatomy has a running plotline about characters pressing the boundaries of 3D to print medical devices, body parts, and in one situation a simulation of a tumor.
The Harvard Business Review has said unambiguously: “3-D Printing Will Change the World.”
The technology has been slowly gaining in sophistication and importance since the early 1980s. But it has really taken off since a key patent expired in 2009.
Today’s subject, though …
How much will it change yachting?
Two and a half years ago, HanseYachts AG, a manufacturer of German luxury vessels, created a 10-meter long hull with its 20 meter long 3-D printer. One of HanseYacht’s senior engineers, Karl Dehler, said at the time: “With the new hull print production we want to manufacture not only more powerful hulls but also reduce the production times significantly in order to satisfy the high demand of our customers. As a result of the 3D print, the Hanse individualization concept can be implemented in every possible way.”
In 2017, Greg Marshall, a prominent naval architect, gave a presentation about 3-D printing at the Superyacht Design Symposium. Marshall said that in due course not merely the hull, or other various parts, but entire Superyachts will be created by printing. The technology will be in place, he said, in little more than another decade, that is, by 2030. It is just a matter of scaling up from what already exists.
How will this affect the industry? There are five important ways. First and most simply, printing (or “additive manufacturing” as it is often called) can be a remarkable cost cutting tool. Standard economic theory indicates that lower costs mean in the first instance higher profit margins, but that those higher margins tempt in new entrants, and the greater level of competition means those margins have to be given back up again — so the cost savings eventually goes to the consumer.
The yachting industry might prove a paradigm case for that theory. After all, and this is our second change, the new technology not only lowers the costs of manufacturing a yacht, it lowers barriers to entry into yacht manufacturing other ways as well, ensuring greater competition.
Thirdly, as both Dehler and Marshall said: the shift to 3-D printing will produce greater customization. It could well become routine for the buyer to participate in the planning of a yacht, right from the blueprint stage, as molds and prototyping become things of the past.
A fourth part of the appeal of the shift to 3-D manufacturing is an environmental one. As Marshall puts it, between 15-20% of the raw material at a shipyard is wasted while a yacht is being created. With 3-D printing, the wastage will fall to just 2%. There is a huge savings in both materials and labor.
Fifth and finally, there is ahead of the industry to prospect of a much quicker turnaround, from the decision to produce a particular model (even an individually customized boat) to its completion and sale.
DUTCH INGENUITY
Let’s return to Martin Logtenberg, which whose CFAM we began. On the WSJ webpage, there is a comment from Richard Welke, professor and director at the Robinson College of Business, Georgia State University.
Welke said “hats off to Dutch ingenuity” but wanted to learn more. He asked for “some analysis of strength [and] CAD-constraints with this plastic/carbon material.”
Logtenberg replied, apparently taking Welke’s question as expressing an interest in a purchase. “We would love to get in touch with you to discuss the possibilities and capabilities of our machine.”
Source: CAT